ブログ_プレゼンテーション『マネジメント向け 品質工学の紹介』2)トラブルの原因は2種類ある [【その他の品質工学関連】]
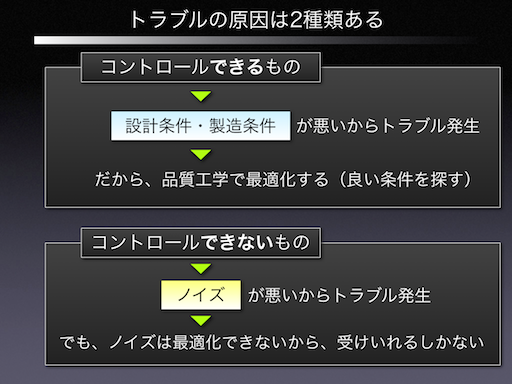
前章「1)技術開発を終えたはずなのに・・・」にて、トラブルの原因には2種類あることを説明しました。
『ノイズ』が悪いからトラブルが発生します。
でも、
『ノイズ』は最適化できないから、受け入れるしかない。
では、どうやって『ノイズ』を受け入れるのかを紹介します。
----------------------
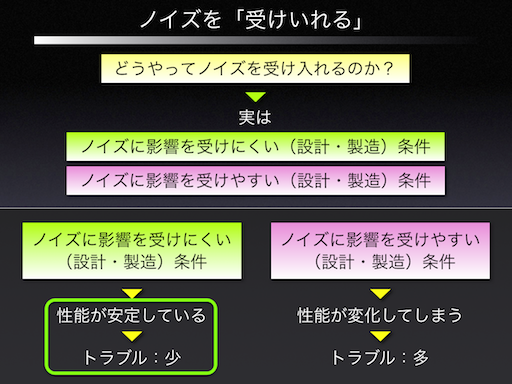
ノイズを「受けいれる」
どうやってノイズを受け入れるのか?
実は、設計条件や製造条件には、以下の2種類の条件があります。
【ノイズに影響を受けにくい(設計・製造)条件】
と
【ノイズに影響を受けやすい(設計・製造)条件】
です。
【ノイズに影響を受けにくい(設計・製造)条件】は、
性能が安定しているので、トラブルが少ないのです。
逆に、
【ノイズに影響を受けやすい(設計・製造)条件】は、
性能が変化してしまうので、トラブルが多いのです。
「性能が安定している」と、なぜトラブルが少ないのだろう?
と疑問を感じる人がいるかもしれませんので、これからその理由を説明します。
----------------------
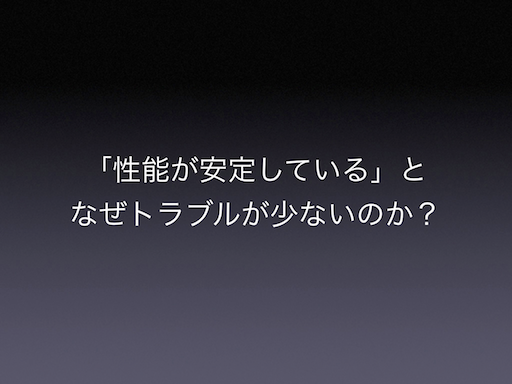
「性能が安定している」と、なぜトラブルが少ないのか?
----------------------

「性能が安定している」と、トラブルは少なくなる理由を、設計と製造の2つの事例で説明します。
設計:エンジンの設計
製造:研削盤の加工条件
----------------------
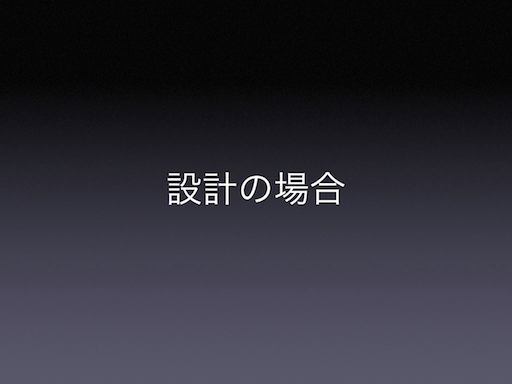
まずは設計の場合です。
----------------------
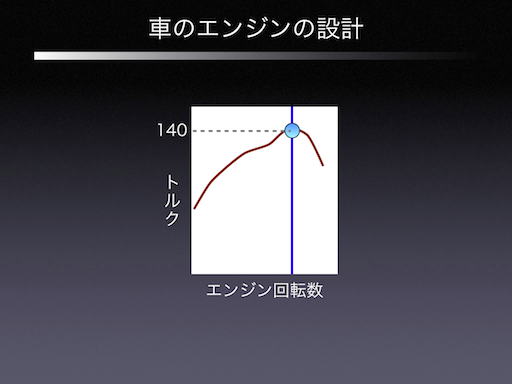
車のエンジンの設計です。
エンジンの性能として、トルクを例に説明します。
このエンジンの最高トルクは「140」です。
----------------------
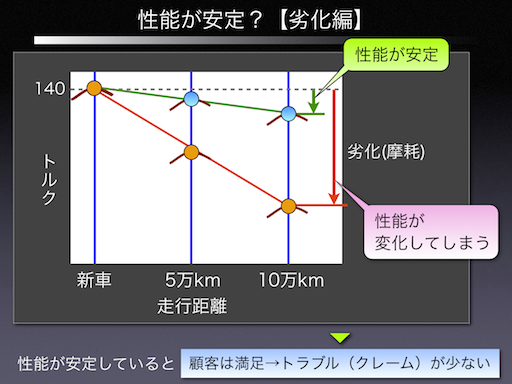
ノイズ「劣化」を例に説明します。
新車の時、トルクは「140」でした。
5万km走行すると、エンジン内部の摩耗や劣化の影響で、トルクは下がってきます。
10万km走行すると、もっとトルクは下がってきます。
このトルクの下がり方が小さい(つまり性能が安定している)方が、お客さんは『このエンジンは劣化が少ない』と好感を抱きます。
逆に、
このトルクの下がり方が大きい(つまり性能が変化してしまう)と、お客さんは『このエンジンは段々パワー不足になってきた』と不満を抱きます。
このように、性能が安定していると、お客さんの満足度は高まり、結果としてトラブル(クレーム)が少なくなります。
つまり、性能が安定していると、トラブルが少なくなるのです。
----------------------
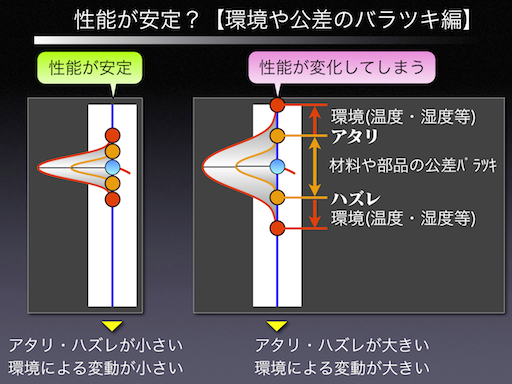
ノイズ「環境」とノイズ「材料や部品の(公差)バラツキ」を例に説明します。
材料や各部品の公差の範囲内のバラツキによって、組み立て上がったエンジンのトルクが変わってきます。
たまたまトルクの高いエンジンが搭載された新車を手にした顧客は、「アタリ」のエンジンを手にして喜びます。
一方、
たまたまトルクの低いエンジンが搭載された新車を手にした顧客は、「ハズレ」のエンジンを手にしてガッカリします。
顧客は、「アタリ」「ハズレ」の大きな車を買いたいと思うでしょうか。
また、環境(温度や湿度)によっても、エンジンのトルクは変動します。
顧客は、晴れの日や雨の日で、エンジンのトルクが変動してしまうような車を買いたいと思うでしょうか。
顧客は、「アタリ」「ハズレ」の小さい車や環境(温度や湿度)による変動が小さい車を望んでいます。
----------------------
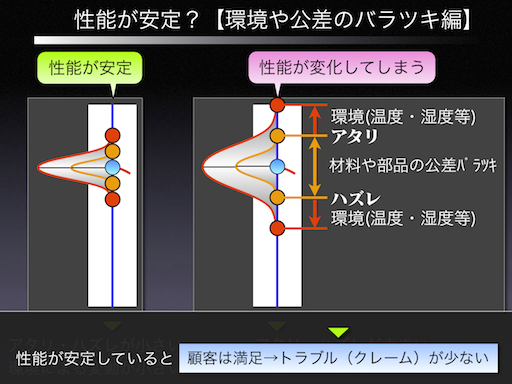
このように、性能が安定していると、お客さんの満足度は高まり、結果としてトラブル(クレーム)が少なくなります。
つまり、性能が安定していると、トラブルが少なくなるのです。
----------------------
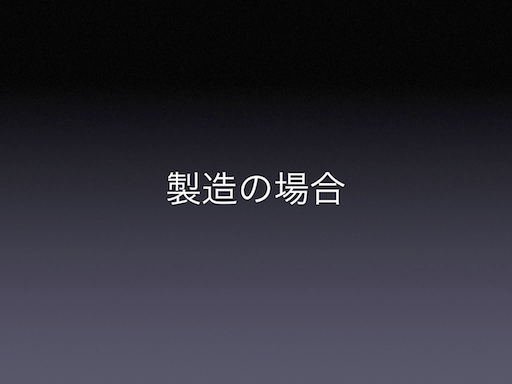
次に製造の場合です。
----------------------
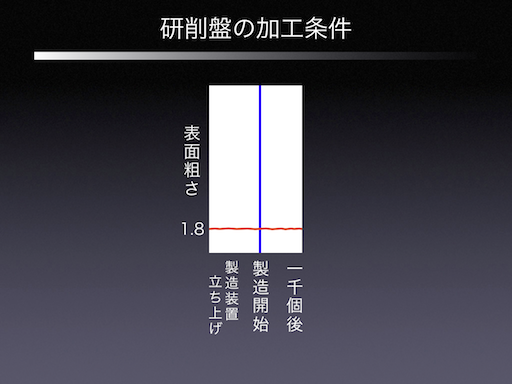
研削盤の加工条件です。
研削条件の性能として、研削後のワークの表面粗さを例に説明します。
この研削盤を使って研削した後のワークの表面粗さは「1.8μm」でした。
----------------------
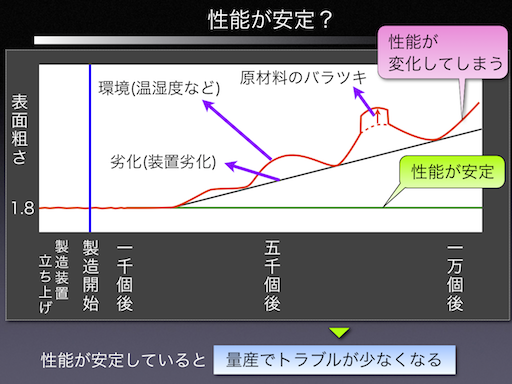
製造装置立ち上げ・製造開始・製造1千個加工後の表面粗さは「1.8μm」でした。
最初に赤い線(性能が変化してしまう条件)について説明します。
5千個加工後の表面粗さは、初期よりも高くなってきました。
1万個加工後の表面粗さは、更に高くなります。
加工個数と共に表面粗さが高くなる原因は、装置劣化です。
また、製造装置の設置環境(温度や湿度)により、表面粗さが変化します。
更に、ワーク(原材料)のロットの(規格の範囲内での)バラツキにより、表面粗さが変化します。
こうなると製造現場は大騒ぎです。
表面粗さを元に戻すべく奔走するわけです。
一方、
緑の線(性能が安定している条件)では、「装置劣化」や「環境」や「原材料のバラツキ」の影響を受けにくいので、最初の表面粗さ「1.8μm」を維持できます。
よって、製造現場はとても平和です。
このように、性能が安定していると、量産でのトラブルが少なくなります。
つまり、性能が安定していると、トラブルが少なくなるのです。
----------------------
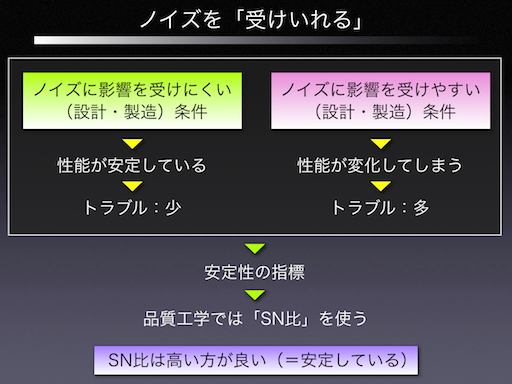
トラブルが少ない、トラブルが多い、という安定性の指標として、
品質工学では「SN比」という指標を使います。
※SN比は高い方が良い(=安定している)
----------------------
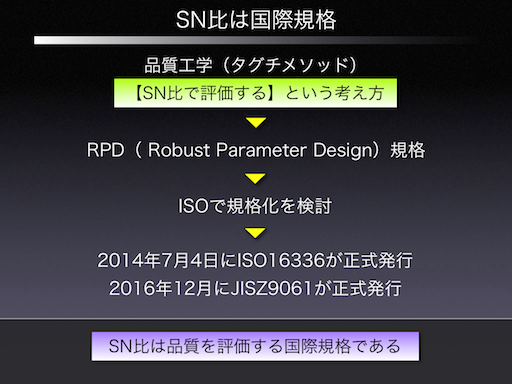
SN比は国際規格。
品質工学(タグチメソッド)の「【SN比で評価する】という考え方」が、RPD(Robust Parameter Design)規格として、長らくISOで規格化が検討されてきました。
そして、
2014年7月4日 に【ISO16336】として正式発行されました。
また、同じ内容のJISで、
2016年12月に【JISZ9061】として正式発行されました。
つまり、
SN比は品質を評価する国際規格なのです。
----------------------
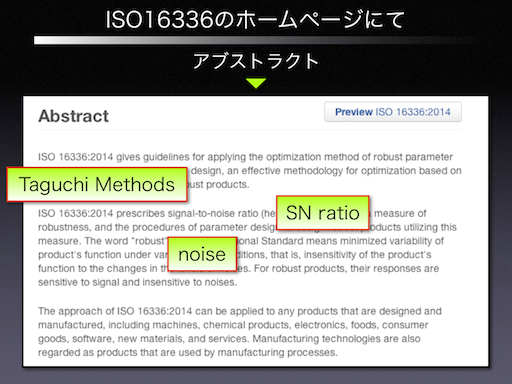
ISO16336のホームページのアブストラクトを見てみましょう。
その中に、タグチメソッド(つまり品質工学)、SN比、ノイズという用語が入っています。
----------------------
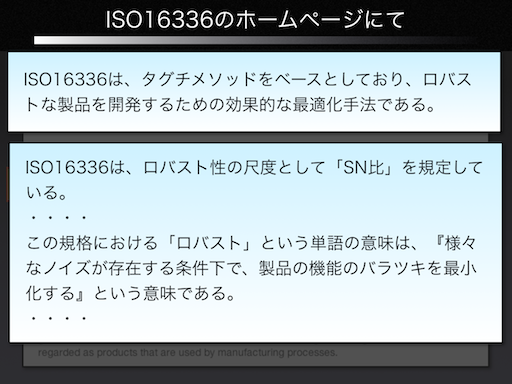
日本語に超訳してみました。
ISO16336は、ロバストパラメータ設計(RPD)の手法を利用するためのガイドラインを提供する。
タグチメソッドをベースとしており、ロバストな製品を開発するための効果的な最適化手法である。
ISO16336は、ロバスト性の尺度として「SN比」を規定している。
パラメータ設計では、この尺度を利用してロバストな製品を設計する。
この規格における「ロバスト」という単語の意味は、『様々なノイズが存在する条件下で、製品の機能のバラツキを最小化する』という意味である。
『様々なノイズが存在する条件下で、製品の機能のバラツキを最小化する』とは、製品の機能をノイズの変化に対して鈍感にすることである。
ロバストな製品には、『信号に対しては敏感で、ノイズに対しては鈍感である』であることが望ましい。
ISO16336の取り組みは、機械、化学製品、電子機器、食品、消費財、ソフトウェア、新材料、サービスなど全ての製品の設計・製造に適用される。
生産技術も同様に、製造工程で使われる製品(製造装置)として扱われる。
----------------------
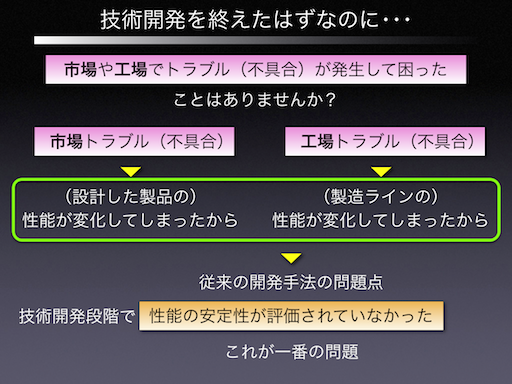
技術開発を終えたはずなのに、なぜトラブルが発生してしまうのか。
それは、
(設計した製品の)性能が変化してしまったからなのです。
(製造ラインの)性能が変化してしまったからなのです。
従来の開発手法の問題点は、正にこれです。
技術開発段階で【性能の安定性が評価されていなかった】ため、市場や工場で性能が変化してしまい、トラブルが発生していたのです。
----------------------
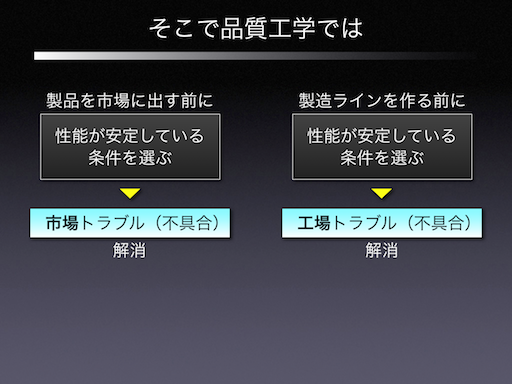
そこで品質工学では、
(製品を市場に出す前に)性能が安定している条件を選びます。
結果として、市場でのトラブル(不具合)を最小化することができます。
(製造ラインを作る前に)性能が安定している条件を選びます。
結果として、工場でのトラブル(不具合)を最小化することができます。
----------------------
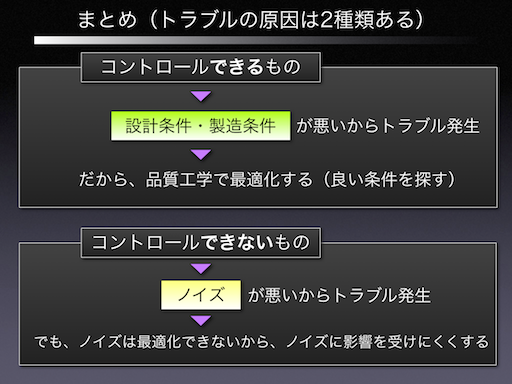
まとめ(トラブルの原因は2種類ある)です。
トラブルの原因は、2種類あります。
1つ目のトラブルの原因は、『コントロールできるもの』です。
具体的には、『設計条件や製造条件』です。
『設計条件や製造条件』が悪いから、トラブルが発生します。
だから、
品質工学を使って『設計条件や製造条件』を最適化する(良い条件を探す)のです。
2つ目のトラブルの原因は、『コントロールできないもの』です。
具体的には、『ノイズ(誤差因子)』です。
『ノイズ』が悪いから、トラブルが発生します。
でも、
『ノイズ』は最適化できないから、ノイズに影響を受けにくい(設計・製造)条件を求めます。
----------------------
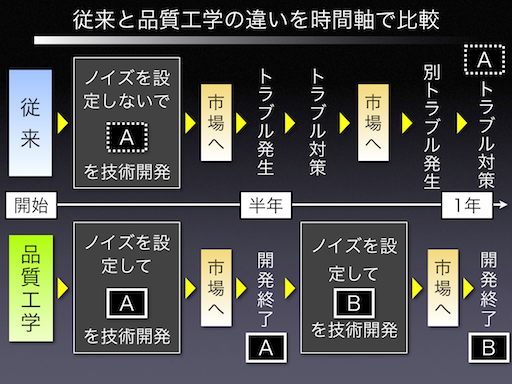
従来の開発手法と品質工学の違いを時間軸で比較します。
※横軸は時間軸です。
※製品の設計で説明します。
従来の開発手法では、トラブルの原因であるノイズを設定しないで「A」という製品を技術開発します。
その製品を市場に投入すると、市場でトラブルが発生してしまいます。
トラブルは放置できないので、トラブル対策をして、市場に再投入します。
しかし、別の所にトラブルが発生し、トラブル対策を繰り返すことになります。
結局、1年経過して、「A」という製品には、まだトラブルが発生し続けています。
一方、品質工学では、トラブルの原因であるノイズを設定して「A」という製品を技術開発します。
ノイズに影響を受けにくい設計条件で作ってあるので、製品を市場に投入しても、殆どトラブルは発生しません。
ということで、半年で「A」という製品の技術開発は終了です。
次に、「B」という製品も同じく品質工学で技術開発をします。
すると、その半年後には同じように技術開発が終了します。
1年経過後の両手法を比較してみると、
従来の開発手法では、「A」という製品には、まだトラブルが発生し続けています。
品質工学では、「A」と「B」という製品の技術開発が終了しています。
品質工学における技術開発の効率化は、このように実現できるのです。
----------------------
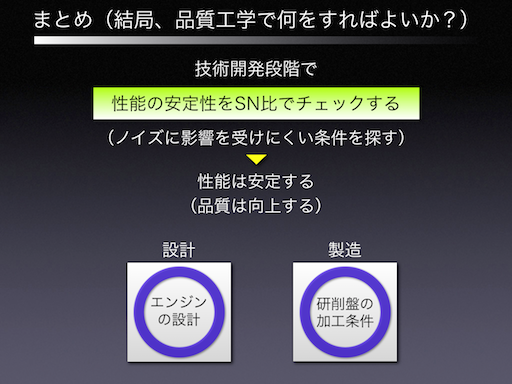
まとめ(結局、品質工学で何をすればよいか?)
技術開発段階で
「性能の安定性をSN比でチェックする」
(ノイズに影響を受けにくい条件を探す)
ことにより
性能が安定する(品質が向上する)
----------------------
以上のような内容をマネジメント層に理解をしてもらえれば、技術者は品質工学を活用しやすくなるかもしれません。
そのために、今回のマネジメント向けの品質工学の紹介プレゼンを作りました。
ご参考になれば幸いです。
【前の記事】←■
【目次】
----------------------
1)技術開発を終えたはずなのに・・・
2)トラブルの原因は2種類ある
----------------------
【お問い合わせ】
----------------------
品質工学またはこのプレゼンに関するお問い合わせは、電子メールにてお願い致します。
(48hr以内に必ず第1報の返信メールを致します)
e-mail:info2qe@abox3.so-net.ne.jp
または、Googleフォームに必要事項をご記入下さい。
----------------------
※弊社の事業内容はこちら
2017-09-17 13:58
コメント(0)
コメント 0